Wire splicing is a mandatory set of activities whose task is to establish wiring in the room. A high-quality connection of the soldered wires, the connection of wires in the distribution panel, the correct twisting - these are factors that determine the durability and performance of electrical wiring.
Advantages and disadvantages of soldering electrical wiring
To properly solder the wires, you need to familiarize yourself with the advantages and disadvantages of the method. Despite existing analogues, this method is considered the most common and in demand, especially in electronics.
Advantages:
- Reliability. An important parameter is the presence and magnitude of the transition resistance. The lower it is, the better. For soldering, this parameter is extremely small. The reliability of soldering is inferior to welding in only one case - if the work had to be performed in extreme conditions, for example, in an environment with an extremely high or low temperature, exposure to aggressive environments. If we are talking about apartment wiring or a country house, such factors are excluded.
- The connection is maintenance free.
- Universality of use. Using soldering, it is possible to connect single-core and multicore wires with different cross-sectional areas, in any combination. This versatility allows you to solve many non-standard and difficult tasks. In addition, the use of fluxes provides a reliable connection of copper and aluminum conductors.
- Low cost of connection. For work, you need a soldering iron, solder and flux. The cost is low and the cost is economical.
Disadvantages:
- Low manufacturability. To carry out the work, many preparatory measures are required, hence the high complexity.
- The need for qualification of the performer.
When soldering, changes in materials occur at the molecular level, so pre-soldered parts are thoroughly prepared.
What you need to solder the wiring
Before soldering the wire, prepare a working tool and consumables. To complete the work, you need the following list of tools:
- An ordinary household soldering iron, the power of which ranges from 40-100 watts. A welding machine is used as an analogue, on which it is possible to control the temperature of the tip, which simplifies the soldering process.
- A small file for cleaning a soldering iron tip.
- Knife to remove the insulating layer.
- Pliers for twisting.
- Rosin intended for tinning the surface.
- Solder for brazing various materials, acid-free fluxes are used as an analog.
- Gas-burner
- Solder
- Pine rosin for soldering
Soldering aluminum and copper wires is somewhat different in the types of solders used.
Copper | Aluminum |
Tin and lead compounds are used. The marking is as follows:
|
|
How to solder wires correctly
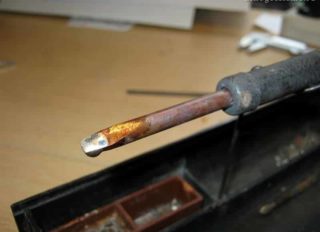
The soldering process may vary slightly depending on the materials used. Different methods involve the use of different solder compositions and fluxes. Most often, the soldering of wires is carried out when connecting copper wires with a cross-sectional area of up to 6 mm.sq.
When performing work, the following algorithm is observed:
- An insulating layer with an approximate length of 5-6 cm is removed from the wires.
- The working tool is heated and the surface is coated with a layer of rosin or flux. The first does not work well on oxidized surfaces, with deep penetration into the twist it is important to carefully process the materials beforehand.
- When warming up a wire using a pre-heated tool with solder on the tip, it is important to achieve uniform distribution of solder over the entire machined surface.
- When soldering the twist, specialists must fill in the solder with all the bumps.
- At the end of the work, all twists are carefully insulated with special nozzles, electrical tape and heat-shrink tubing.
If you want to work with aluminum, it is important to consider its high oxidation rate when in contact with oxygen. The resulting film does not allow a reliable adhesion of the metal to the solder.
The oxide is removed mechanically, then the surface is maintained. The algorithm for connecting aluminum conductors depends on the type of flux used and the cross-sectional area. For heating, as a rule, use a gas burner.
The order of soldering conductors with an area of 4-10 mm.kv:
- At the ends of the cores 5-6 cm long, the insulation layer is removed.
- To obtain a metallic sheen, the veins are stripped with a file, sandpaper or a knife.
- The veins are connected to each other with an overlap by a double twisting method, a groove is made at the point of contact in the middle.
- The junction is heated to a temperature that is close to the melting point of the solder.
- In a similar way, each side of the twist is processed, all cavities are filled with tin.
- At the end of work, the junction is cleaned with gasoline.
- The cleaned surface is covered with asphalt varnish and carefully insulated.
The work does not differ in speed, but the high quality and durability of the connections is worth the time and effort.
How to solder copper and aluminum wires
The copper wire is carefully peeled, then immersed in rosin. The specialist melts a few drops of solder and for tinning the wire is immersed in the molten mass. The procedure is performed with careful and uniform movements.
Solder for soldering should cover the surface of the wire as little as possible. The excess is removed with a hot soldering iron. During the work, the red shade of the copper wire should change to silver.
If you have to work with multicore soldering irons, each wire should be untwisted and only after it is torn. Further, everything returns to its original position.
Before the soldering of electric wires, the aluminum wire needs to be stripped, after which the previously prepared flux is evenly distributed on its surface. Next, the aluminum wire is carefully rubbed with a small piece of tinol and heated by the flame of a gas burner. Such manipulations will effectively get rid of the oxide film.
To increase the quality index of the connection of single-wire wires, twisting of tinned wires of small sizes is used. All cavities formed are filled with tinol.
The next step is the connection of copper and aluminum wires. To do this, restore the insulating layer. For dry rooms, only cotton tape can be used.
Recommendations, precautions
You should familiarize yourself with the recommendations that will allow you to qualitatively perform the tasks:
- When choosing a soldering iron, you need to pay attention to models equipped with additional cones, needles and a set of interchangeable tips.
- Before proceeding with the soldering, special attention should be paid to stripping the tip.If the tip is too dirty, remove all dirt with a soldering iron. You can optionally use pieces of wood or cardboard.
- When changing the length of the soldering iron, the temperature of the heating of the tool also changes.
- While heating the working element, it is not recommended to leave the soldering iron “dry”. You need to regularly lower the sting into the rosin.
It is important to observe safety precautions. You need to work in personal protective equipment: special clothing (special clothing), glasses and gloves. Do not leave exposed areas of the body, otherwise severe burns may form.