Energy conservation issues are equally relevant for residents of private homes and city apartments. Even with central heating, the thermal insulation of the walls can significantly improve the indoor microclimate by reducing humidity and temperature drops. For private apartments, the amount of heating fees directly depends on the quality of insulation for the house and the correctness of their installation. This procedure can be performed independently or with the assistance of specialists. The choice depends on the complexity of the technology and your own building skills.
Types of materials for insulating walls outside and inside
The construction market offers a wide range of materials that vary in appearance, performance, cost and installation methods. When choosing, you need to take into account all the structural features, climate, weather and your own financial capabilities. When purchasing insulation for walls, it is necessary to take into account the aesthetic side so that the isolated structure blends in seamlessly with the surrounding landscape.
To make the right decision, you should familiarize yourself with the presented products, evaluating all its advantages and disadvantages.
Polyurethane foam (PPU)
A new generation of modern heat insulators is becoming increasingly popular in private and industrial construction.
Polyurethane foam is a mixture of two solutions, which are applied under high pressure on the treated surface. Thanks to the use of a compressor and atomizer, the substance is delivered to flat surfaces and to any inaccessible places.
After solidification, forms a layer of spongy substance with excellent performance.
Insulation for the walls of the house has the following advantages:
- low thermal conductivity;
- good sound insulation;
- water resistant
- lack of hygroscopicity;
- long service life (30-50 years);
- immunity to temperature extremes;
- resistance to aggressive chemicals;
- low specific gravity;
- excellent adhesion to any surface.
The material also has disadvantages. Polyurethane foam quickly deteriorates under the influence of ultraviolet radiation. Immediately after application to the surface, it must be covered from the sun. From a technical point of view, there are also difficulties - for the thermal insulation of PPU, special equipment is needed, plus the high price of raw materials. Based on this, the estimate for the arrangement of the object will be large.
Mineral wool

Mineral wool is a dense slab of thin and long fibers obtained from the processing of rock and blast furnace slag. Depending on the production technology, the material acquires a corrugated, vertically layered and horizontally layered structure. Finished products vary in shape, size and thickness. Available in the form of plates and rolls. The most popular product today is basalt cotton wool of the Knauf and Technonikol brands.
Plate material has the following advantages:
- low density;
- fire resistance;
- free transmission of air and steam;
- excellent absorption of noise and vibration;
- simplicity and speed of installation;
- mold and mildew resistance
- elasticity, providing tight fixation in the grooves;
- unlimited service life.
The disadvantage of a thermal insulator is its tendency to shrink. Over time, its volume decreases, there is a likelihood of gaps. To prevent wetting of cotton wool, the installation of vapor barrier membranes is necessary.
Glass wool
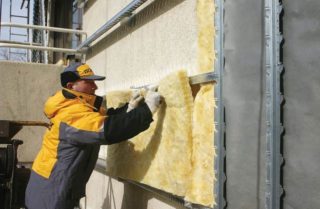
The manufacture of insulation is carried out from glass battle with the addition of limestone, soda and dolomite. The products are manufactured in the form of rolls with a strip width of up to 200 cm. To improve operational characteristics, the base is made of foil, cardboard or fiberglass.
Material Advantages:
- affordable cost;
- resistance to high temperatures;
- softness and flexibility;
- durability;
- ease of installation;
- biological inertness.
Glass wool has more disadvantages than stone and slag analogues. It absorbs moisture well, while losing insulation properties. During processing, the fibers break, which adversely affects the insulating properties of the coating.
Plate heaters
When choosing materials for insulation for the home, it makes sense to think about polystyrene-based boards. Polyfoam is very popular in the implementation of internal and external insulation of country houses and outbuildings. Moisture-resistant material has several advantages that could not go unnoticed by builders.
Advantages of foam:
- ease;
- low price;
- ease of installation;
- average service life up to 50 years;
- resistance to chemicals;
- low thermal conductivity.
Please note that the plates do not conduct steam and air. Polyfoam is not recommended to insulate the walls of wooden structures from timber, logs and shields. At the same time, it is great for laying on the floor and ceiling. In the insulation, rodents and insects can start.
Basic material selection criteria
When choosing heat-insulating materials for walls, it is necessary to take into account the place and technology of their installation. In some cases, you can limit yourself to one type, and sometimes for the work you need several varieties of insulation.
You should adhere to such selection criteria for wall thermal insulators:
- lack of shrinkage;
- low thermal conductivity;
- ease of installation;
- resistance to temperature extremes;
- immunity to dampness;
- long term of operation.
When deciding how to insulate a summer cottage, one should dwell on solid materials that are distinguished by mechanical strength and water resistance. When arranging wooden buildings, it is necessary to use steam-conducting heaters for the exterior walls of the house so that excess moisture can freely come out of the room. Foamplex having a spongy structure with open cells is best suited for such purposes. If you need to insulate a steel garage or a concrete cellar, you should choose polystyrene foam with a thickness of 5 cm or 10 cm. This insulation for a house from the outside will perfectly cope with the thermal and waterproofing of the building.
Pros and cons of external thermal insulation
The outdoor version of insulation has the following advantages:
- The useful volume of the interior is maintained. Given that most private buildings consist of small rooms, this is significant.
- All work is carried out on the street. The house is clean and tidy, there is no need to move things and change the way of life in connection with a forced temporary relocation. There is no risk of contaminating things with dust and mortar.
- The supporting structures are isolated from the damaging environmental factors - moisture, ultraviolet radiation, temperature drops, birds and insects. The dew point is shifted from the walls to the width of the insulator.This helps to extend the life of the building and create a comfortable microclimate in it.
Cons of this technology:
- Work must be carried out in good weather at certain times of the year so that the base dries well and is in a stable condition.
- If the building is tall, you must buy or rent sustainable scaffolding. This entails additional costs and carries the risk of an accident.
- Insulation for exterior walls changes the appearance of the building. He hides a beautiful brick, an array of wood.
The use of original decorative decoration makes it possible to design the facade of the building in accordance with its priorities, using siding that imitates natural and artificial materials.
Inside wall insulation technology
Even if people do not plan to visit the country often, the building needs to be insulated. It must be protected from dampness, freezing in winter and excessive warming in summer. Depending on the size of the room, a frame or adhesive method of arrangement is chosen. Each of them has its own characteristics, advantages and disadvantages.
On glue
This technology is good in that it allows the use of thin wall materials, so that at maximum efficiency a lot of useful room area is not taken.
When choosing the thermal insulation of the walls from the inside, the following materials can be used:
- ceramic plaster;
- foam sheet;
- Styrofoam.
In most cases, a plate material is selected that has good insulation characteristics and is easy to install.
The work is performed in the following sequence:
- Foundation preparation. All objects are removed from the walls, fasteners are unscrewed, switches and sockets are dismantled. Then the old coating is removed.
- Processing of the bearing surface. First, it is covered with an antiseptic, then a liquid primer. It is necessary to wait until the walls are completely dry.
- The glue is kneaded, after which it is applied to the insulation boards. This should be done with a notched trowel to ensure a smooth and tight fit.
- Each subsequent row is stacked with an offset of half the sheet. The edges and top are trimmed to fit.
- The remaining slots are blown with foam or sealed with scraps of material.
- A polymer mesh is adhered over the coating. The strips overlap each other with an overlap of 15-20 cm.
- A putty coat is applied over the mesh. After complete drying, the surface is polished and treated with a primer 2-3 times.
The final step is to apply the finish. Depending on the priorities of the owners, water-based paint, non-woven or liquid wallpaper, cork or ceramic tiles are used.
On the frame
This technology is used in cases where mineral wool or polyurethane foam is used as a heat insulator.
Work sequence:
- Boards are prepared for the frame. The elements are well dried, then treated with antiseptic and impregnation.
- The wall is cleaned of foreign objects and treated with an agent against fungus and mold.
- A membrane web is nailed to the surface. Joints of strips are sealed with aluminum tape.
- Boards in a vertical orientation are attached to the wall. The distance between them should be 3-4 cm less than the width of the mineral wool. For foam, the best option is 100 cm.
- Insulation is applied. Plates are inserted by surprise, the foam is sprayed from bottom to top with a thickness of each layer up to 5 cm.
- Another web of membrane film is attached.
- Drywall is screwed on the frame. The joints are sealed with a mesh, the recesses from the heads of the screws are smeared.
- The surface is primed and plastered. After the putty is dried, it is polished and primed.
The final step is to finish the walls in accordance with the repair project.