One of the ways of home insulation is polystyrene foam sheathing. The material is not very expensive, installation is quite acceptable to do on their own. It is possible to protect the casing from the negative influence of the external environment with the help of a suitable coating. A good option is facade polystyrene stucco, which does not require large expenditures.
Advantages of Styrofoam
The material is used to perform thermal insulation, 98% consists of air. Outwardly, it is similar to polystyrene, but in other parameters these heaters are different. Polystyrene foam boards are widely used for noise insulation and wall insulation.
Main advantages:
- strength;
- resistance to moisture;
- high level of thermal insulation;
- vapor permeability;
- there is no reaction with cement, so polystyrene boards can be plastered;
- does not contribute to the development of fungi, mold;
- under conditions of proper operation, the service life reaches 30 years.
An external protective layer of plaster can be laid on the surface of this material.
Types of Coatings
In practice, plaster facades with polystyrene foam can be of several types.
Mineral
They are made on the basis of slaked lime and Portland cement with the addition of stone chips and sand, for example, “bark beetle”, “fur coat”. They differ among themselves only in texture, which is achieved thanks to different types of fractions of pebbles in the filler.
Pros:
- resistance to natural factors: humidity, ultraviolet, sudden changes in temperature;
- high vapor permeability;
- absence of toxic fumes even under the influence of high temperature;
- good adhesion.
There are mineral-polymer mixtures for external polystyrene plastering. In them, polymer resins are added to the cement base. This slightly increases the price of the composition, at the same time significantly improves the elasticity of the coating and increases the service life.
Acrylic
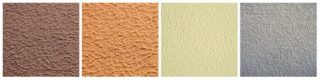
The basis of the plaster is sand, stone chips, a coloring element, water-repellent additives. Acrylic resins act as a binder.
Decorative plaster on extruded acrylic-based polystyrene foam differs in the following qualities:
- excellent moisture resistance;
- good elasticity, which eliminates the likelihood of cracking;
- impact resistance;
- a huge selection of shades;
- the possibility of painting the facades after finishing;
- high adhesion to external coatings;
- aesthetics;
- long service life.
A significant disadvantage of acrylic coating is its high price.
Dyes, which are part of acrylic plasters, are unstable to ultraviolet radiation. For this reason, over time, the color will fade.
Styrofoam plasters
Expanded polystyrene facade plaster is in great demand, since it has many positive properties:
- Strength. Due to its qualities, it reliably protects the structure from harmful factors.
- Frost resistance. If you do not pay attention to this indicator, then under the influence of frosts the coating may crack.
- Long term of operation. Facade stucco on polystyrene foam can last up to 15 years.
- Vapor permeability.The ability to remove condensate prevents the destruction of the finish and the formation of mold, fungus.
- Ease of installation, care. If desired, you can apply the coating yourself. Special care for the material is not needed.
Thanks to the listed properties, the plaster ideally lays on the insulation, performs decorative, protective functions.
Preparation for work
Before plastering polystyrene foam, you need to purchase the necessary tools and ready-made mixtures.
To cover the walls you will need:
- grater;
- a small container for the preparation of the solution;
- mixer or drill with pad;
- construction grid;
- sandpaper for grouting;
- putty knife;
- level;
- Master OK.
Materials:
- plaster mix;
- primer;
- mixture of decorative coating.
To protect polystyrene foam, special compounds are produced, on which the result of future work depends, the duration of use of thermal insulation.
Solution preparation
The mixture is prepared strictly according to the manufacturer's instructions.
Within the same building, a solution of a single manufacturer is used. Ignoring this rule may reduce the quality of the entire coverage.
The calculation of the consumption of universal plaster: from 4 kg / m2 - for fastening reinforced mesh, up to 6 kg / m2 - for the final alignment of the external walls of the structure.
The mixture should be diluted to a liquid so that it drains from the spatula.
Styrofoam plaster technology
For reliable fixation of the coating, it is necessary to use an internal mesh. Otherwise, the coating will not last long.
Reinforcing mesh
A dense insert is more suitable for working with insulation, since plaster is better placed on it. But in this case, it’s harder to work with corners. The best option is a grid with a density of 140-150 g / m2. First of all, they begin to trim the slopes of the room.
The order of installation of the reinforcing material at the corners:
- The grid is cut into 1-meter stripes, which are bent inside.
- A solution is applied to the wall. The coverage area should correspond to the size of the cut strip.
- Apply reinforcing material to the corner, smooth with a spatula. The latter should move from the upper to the lower, from the central region to the extreme.
Thus, the entire grid is covered with a layer of plaster.
The installation of reinforcing elements on the walls is as follows:
- The grid is cut into pieces about a meter long. Sequential fastening is done in small pieces, because the mixture dries quickly enough.
- A solution is applied to the area of one area, onto which a piece of the grid is laid out, leveled, fixed with the help of smoothing movements with a spatula.
- In case of incomplete immersion of the reinforcing material, the solution is applied again.
Similar work is gradually being done in the following sections of the wall.
Surface grout
The procedure is performed after drying the walls with sandpaper, grater. After previous work, it can be started after 2-3 hours on warm sunny days, in a day on cloudy days.
Grout make movements in a circle. If wet plaster gets on the paper, it must be replaced.
Alignment
The next stage of work is the application of a leveling layer, the primer of the surface.
- With a small spatula, put the solution on a large one.
- With leisurely confident movements, the mixture is applied to the surface of the wall.
- After drying of the applied layer of the solution, grout is done (no later than the fourth day after the previous stage of work).
- It is treated with an antifungal primer using a roller to prevent mold.
After the primer dries, you can start decorating.
Decorative plaster
To perform work outside there are special mixtures that are resistant to sudden changes in temperature. Their properties depend on the binder, additional elements.
The sequence of decorating plaster:
- Prepare a working solution.
- Apply a layer of plaster (not more than 4 cm). The next one is applied only after the previous one dries.
- Grouting is done if the plaster is half-dried (fixed, but correctable).
The application of the decorative layer can be performed under the following weather conditions:
- temperature - 10-25 ° C;
- humidity - does not exceed 70%;
- There are no strong gusts of wind.
The special structure of the facade is made out with a roller of a special shape.
Famous brands
Cement plasters for external use must withstand the effects of the external environment, temperature fluctuations. For this reason, they are especially important indicator of frost resistance, strength.
Ceresit
The compressive strength (a characteristic indicating the ability of the material to withstand loads, withstand damage) is 8 MPa. Frost resistance - about a hundred cycles of freezing and thawing.
Knauf
It has all the properties of Ceresit. The difference is only in lower compressive strength (7, 5 MPa) and frost resistance (75 cycles).
Will establish
Plaster mixes have high strength - 10 MPa, frost resistance - 75 cycles. In the series there is a variety of types of plasters: winter, reinforced, high strength.
Plastering polystyrene foam slabs is an excellent way to protect against adverse external influences and create an attractive type of structure. The stucco technology for extruded polystyrene foam is quite simple. If desired, it can be easily mastered and performed on its own.